I realized that the last time I mentioned my home server, it was when I switched away from unRAID. I did so because I really wanted dual-drive redundancy, and more powerful options for running services other than basic file-sharing on it. That was some years ago, and I’ve since switched back to unRAID, because starting with version 6, it basically checks all the boxes. It now supports dual-drive parity, mirrored cache drive pools, and a very impressive collection of software add-ons made possible by docker. I’m very happy with it.
Case-wise, I think I started out using an old Antec P180 tower case, then moved things into the Norco 4U rackmount case mentioned in the older posts. It was dirt-cheap for rackmount gear, and it was just impossibly loud. You could easily hear it from another floor of my house. But it was cheap, and fit a lot of drives, and like a lot of hobbyists, all I really want is enterprise-grade hardware for cheapo prices.
After the Norco case, I moved things into the NZXT H2 tower case; I could fit 13 3.5″ hard drives into it along with a few SSDs, and it was nearly silent. I ended up making my own SATA power cables for my modular power supply to clean up the airflow inside. A nice case, but once I moved into a place where I could stash the server in the basement, I was ready for something bigger. I briefly expanded by picking up a dual external-port SAS controller card, and connecting it to a couple of 4x drive pods in an old multi-drive SCSI enclosure — you can get replacement plates for the back that swap out the old SCSI connectors with SAS, eSATA, USB, or whatever.
After doing some research online, I concluded that the cheap enterprise-grade solution I was looking for was used Supermicro gear. I really liked the look of the 933T chassis, a 3U server with 15 vertical hard drives lined up in a row. They’re all hot-swappable with a SATA backplane. (There are SCSI and SAS backplane options, but I believe the SAS version requires interposers for SATA drives, so whatever.) The 933T occasionally showed up on eBay for ~$150, often with an old Opteron-based motherboard. One nice feature of Supermicro’s hardware like this is that it’s all ATX standard, so you can swap it out for whatever else. The included power supply supported 3 redundant hotswap PSU modules, so that’s a plus.
It was pretty noisy, so I swapped out various fans (including some 40mm fans in the PSU modules, probably the noisiest of them). Now it’s nice and quiet.
Another nice feature of Supermicro stuff is that they sell a ~$20 board designed to convert an ATX server case into a JBOD drive enclosure; it hooks up to the ATX power connector and various case connectors (power & reset button, power LED, etc.) and lets you power on/off the device without a full motherboard in it. So I bought two 933T’s! One of them contains the motherboard (an Intel DZ77GA-70k) and SAS controller, the other contains the JBOD “motherboard” and a SAS expander hooked up to the backplanes. So now I have a quiet 6U server with room for 30 hotswappable drives.
I built a simple wooden rack using some 12U brackets to put everything in, and eventually added in a couple of 2U UPS’s and an old 1U console. At some point I’d like to replace the rack with something solid (with removable panels), but otherwise I’m thrilled with the current arrangement.
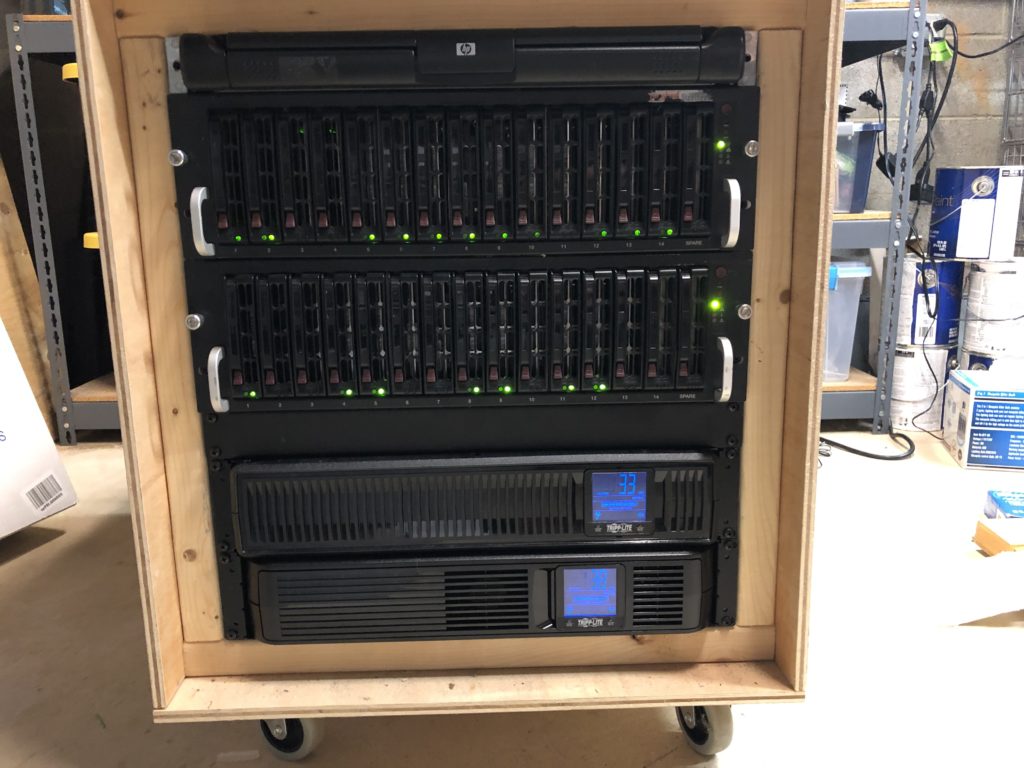